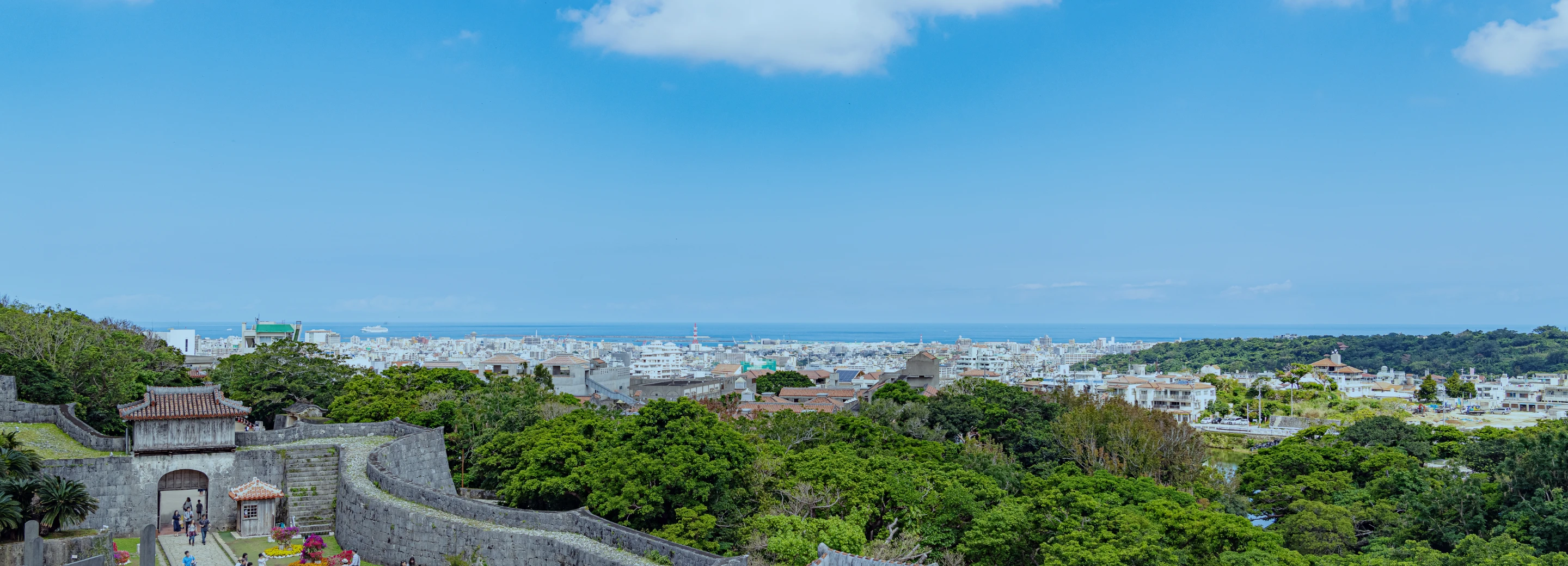
TOPIC
トピック
- ホーム
-
Total Quality Management TQM: Definition, Principles & Examples
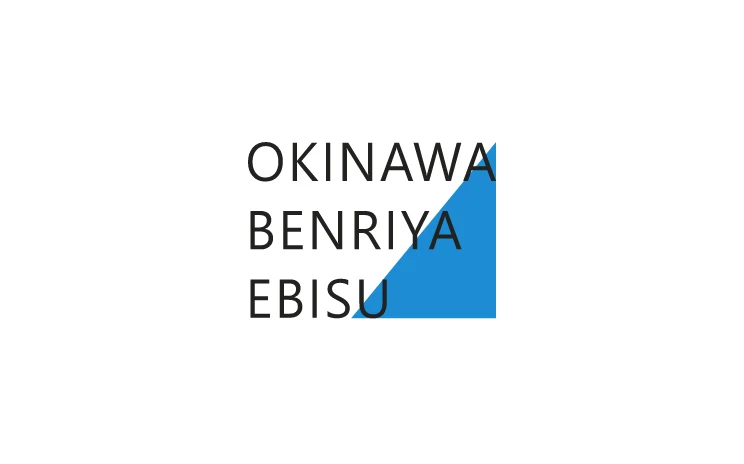
2021.09.16
Total Quality Management TQM: Definition, Principles & Examples
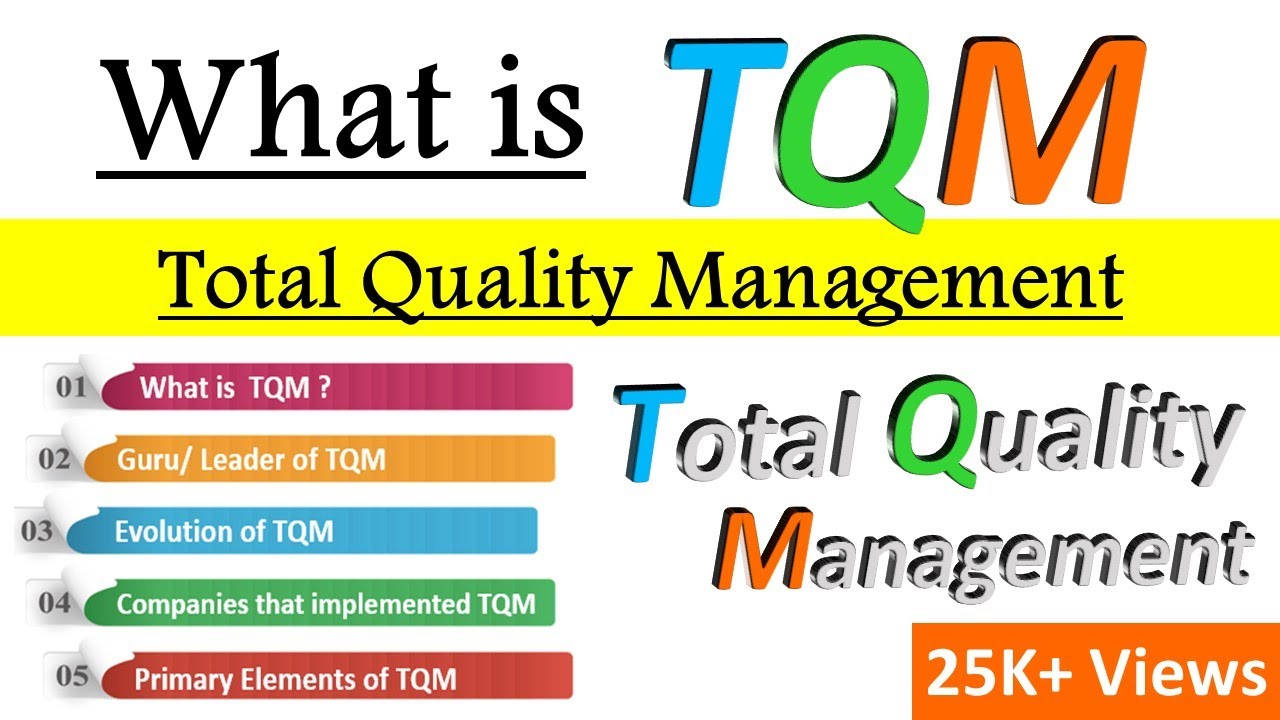
This strategy focuses on using the criteria of a reputable TQM quality award to identify areas of improvement. It’s essentially using the rubric for awarding the prize as a guide to discovering and implementing changes within a business because the award criteria define success. Although well-known in academic quality control circles, he achieved greater prominence when he was interviewed for the 1980 NBC documentary “If Japan Can, Why Can’t We? ” In the program, Deming emphasized that, “If you get gains in productivity, it is only because people work smarter, not harder. That is total profit, and it multiplies several times.” The documentary revealed another act in Deming’s life, that of a sought-after quality consultant to American business.
Improved Customer Satisfaction:
Here’s how BIM transforms workflows, enhances collaboration, and enables construction and infrastructure firms to scale up without sacrificing quality. For small firms in the construction and infrastructure sectors, competing with larger, established companies often feels out of reach. Limited resources, outdated workflows, and constrained budgets can make it challenging to match the service quality of major industry players. With BIM, small companies now have access to the same tools as larger corporations, empowering them to deliver high-quality, efficient results on par with those of the bigger competitors.
The Benefits of Total Quality Management (TQM)
This can lead to increased engagement and motivation, as employees feel that they are working together towards a common goal. Continually collecting and analyzing the most up-to-date performance data on your business is a vital part of TQM. Data collection and analysis improve the quality of your decision-making and forecasting abilities. It means making sure everyone in the company knows what’s going on, understands the quality goals, and knows how they can contribute. It’s about making sure messages are clear, so everyone is on the same page and can work together effectively.
The Principles of Total Quality Management
In the 1960s, quality circles began appearing in Japanese workplaces to allow employees the opportunity to discuss problems and consider solutions, which they then presented to management. Starting on the factory floor, quality circles spread to other functional departments. The company-wide focus on quality may also provide a clue to the origin of the phrase total quality. A company should gradually evolve and strive for incremental, small improvements as it learns more about its customers, processes, and competition.
Total Quality Management
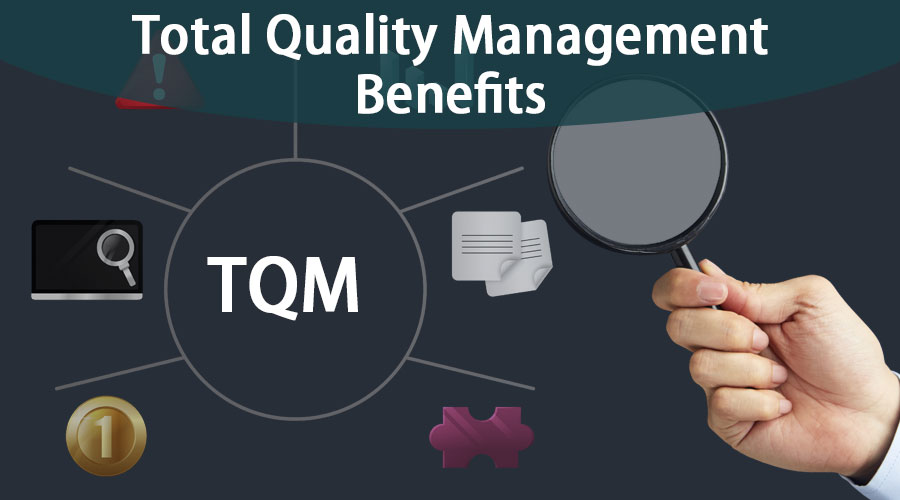
Continuous improvement and a strategic approach eliminate inefficiencies, waste, and defects that degrade products. The adoption of TQM and Kaizen at Toyota led to higher product what is the distinction between debtor and creditor and work quality at all levels of the organization. In 1951, Toyota launched the Creative Idea Suggestion System, which was based on a suggestion system used at Ford.
- Total Quality Management (TQM) can increase profitability and reduce costs by improving efficiency and productivity, reducing waste and defects, and increasing customer satisfaction.
- A company may be required to replace processes, employees, equipment, or materials in favor of an untested, partially developed TQM plan.
- As TQM prioritises delivering good-quality products/services, consumers hold a favourable reputation for the organisation.
- It's important to note here, too, that total quality management isn't always known by that name in the 21st century - despite its original principles and tenets living on.
By continuously monitoring and improving processes, TQM helps organizations to identify and resolve any issues that may be impacting customer satisfaction. Total Quality Management is a dynamic, evolving approach that integrates quality into every aspect of an organization. By focusing on continuous improvement, customer satisfaction, and involving all employees in the quality process, TQM helps organizations achieve long-term success and remain competitive. TQM focuses on consistently improving the process to deliver high-quality products that satisfy customers and benefit organizations and employees. To apply TQM effectively in business for increased efficiency and profitability, professionals in project management must develop the necessary experience and skills. This management approach is used to simplify supply chain management, as well as to detect, reduce or remove errors.
The benefits of TQM—improved quality, increased efficiency, cost reduction, employee satisfaction, and competitive advantage—are substantial. These advantages highlight why TQM is not just a good practice but a strategic necessity for organizations aiming for long-term success and excellence. The journey toward total quality is ongoing, requiring dedication and commitment at all levels of the organization, but the rewards are well worth the effort.
You’ll also have the bonus of potentially winning an award for your execution of the TQM strategy. The chart below is a common example of a TQM flowchart that managers use to decide a course of action and understand business performance in relation to customer needs. Management stems from managers and executives overseeing the process, identifying errors to be fixed, and improving efficiency.